Understanding Piezoelectric Pressure Sensors and Piezo Pressure Vacuum Gauges
Piezoelectric pressure sensors use a specialized material to create a small voltage when mechanical stress is applied to it. In this blog we will explain the principles behind the Piezoelectric pressure sensor, review its specific attributes and then discuss how it is used in vacuum gauge technology and industry applications.
Piezoresistive Pressure Sensors
A Piezoelectric pressure sensor functions on the principle that when mechanical stress is applied to a piezoelectric crystal, an electric potential is generated which is directly proportional to the pressure applied. A vacuum gauge that uses a piezoelectric pressure sensor typically houses the sensor in the diaphragm. This provides good linearity for vacuum transducers as the output signal correlates to the applied pressure. This signal is then used to produce an output voltage that is converted to a pressure measurement. Piezoelectric sensors are rugged and often used for measuring dynamic pressure. Because Piezoelectric sensors have a high sensitivity to dynamic changes in pressure, they are well-suited to the measurement of small changes, even in very high-pressure environments. Although they have a high sensitivity to dynamic pressure that can also be used to measure static pressures.
Piezoelectric pressure sensors are typically used for measuring atmospheric pressure but can be paired with additional vacuum, pressure sensor technologies to create a wide-range vacuum gauge capable of measurement from vacuum to atmosphere. In some cases, a wide-range vacuum gauge can be further expanded upon by adding a 3rd technology to provide a compact solution capable of wide-range measurement from atmospheric pressure to ultra-high vacuum.
"Direct" and "Indirect" Vacuum Pressure Gauges
In vacuum technology, pressure measurement is accomplished using either “Direct” or “Indirect” methods. Direct gauges are so-called because they directly measure the force imparted on a surface. Based on the formula: P = F /A (pressure (P) equals force (F) per unit area (A), the gauge directly measures the pressure. Some examples of direct gauges include: bourdon gauges, capacitance manometers and Piezoelectric gauges.
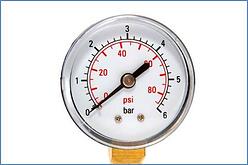
Bourdon Gauge
One of the primary benefits of a direct vacuum gauge is the ability to make accurate measurements regardless of gas type. For example, if the system has 20 Torr of argon, helium, methane, or air, a direct measurement gauge will read the same pressure. Because of this attribute, direct gauges are referred to as “gas composition independent”. These are helpful to see the operating pressure being used during the process.
Indirect gauges do not “directly” measure the force associated with the gas in the chamber. Rather, these gauges measure a property associated with the gas. For example, thermocouple vacuum gauges measure the thermal conductivity of the gas, which is a function of the pressure. Another example of an indirect gauge is the pirani vacuum gauge which measures the pressure-dependent thermal conductivity of the gas in a vacuum using a heated element, such as a wire or thin-film membrane. The heated element is part of a resistance bridge. The temperature, and thus the resistance of the heated element in the vacuum, changes as the pressure changes. By measuring the electrical behavior of the bridge, the pressure in the vacuum can be determined. Consequently, thermocouple and Pirani vacuum gauges can both be called indirect gauges.
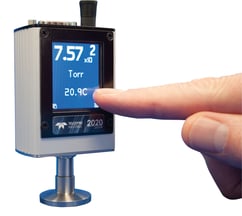
Thermocouple Gauge Pirani Gauge
Application: Vacuum Pressure Impregnation (VPI) Systems
Teledyne Hastings uses piezo sensors for pressure measurements in our HVG-2020A and HVG-2020B vacuum gauges. The HVG-2020A vacuum gauge uses a Piezoelectric sensor that provides accurate pressure measurement throughout the rough vacuum region. The HVG-2020B is a dual-sensor vacuum gauge that uses a Piezoelectric sensor and a Pirani sensor to measure a wide range.
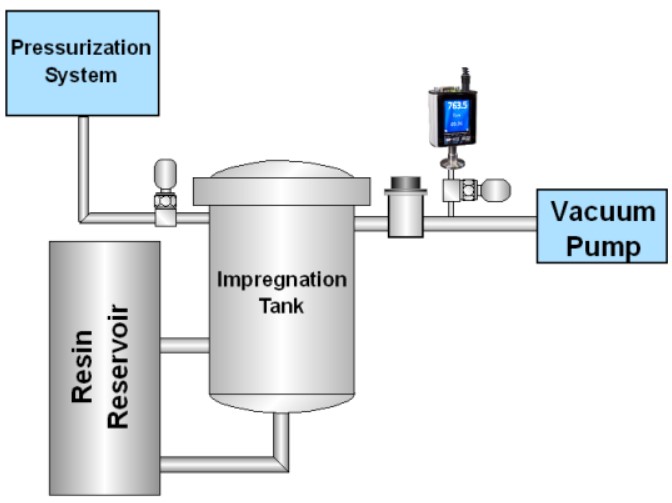
Because the HVG-2020A measures from 0.1 Torr to 1000 Torr, it is well-suited to vacuum pressure impregnation (VPI) applications. Vacuum pressure impregnation (VPI) is an important application for applying insulating materials, as well as producing void-free castings. A typical example is the encapsulation of windings in electric motors. If an insulating resin is simply “painted” on a winding, the result will be a network of uninsulated voids between the winding layers. Applying pressure may force some insulation into the voids, but the subsequent release of that pressure will cause the trapped gas to expand again, causing voids to reappear.
These voids in the insulation can lead to motor failure due to movement of the wiring during operation. Also, in high-voltage applications, these air-filled gaps can serve as sites for corona discharge formation, leading to losses in efficiency and resulting in further weakening of the dielectric.
The proper method to prepare windings, and other potted devices for impregnation, is to begin by applying vacuum.
- The first step is to load the assembly into a vacuum/pressure chamber and apply vacuum to remove air from the voids between the windings. A suitable pressure for this step is 5 Torr.
- The next step involves a two-part soak. While under vacuum, the insulating resin is introduced into the chamber from a storage vessel. The vacuum provides the additional benefit of removing any air bubbles that may be present in the resin. After a dwell period, the chamber is pressurized to 85-95 psig for another period of time. This pressurization forces the resin into the previously evacuated voids in the winding layers.
- After another dwell period, the pressure is relieved and the surplus resin is returned to the storage vessel. With the chamber at atmospheric pressure, it is opened and the assembly is removed. This process results in void-free application of the insulating resin on the windings.

Teledyne Hastings: HVG-2020A Vacuum Gauge
The Teledyne Hastings’ HVG-2020A vacuum gauge is a media-isolated, gas composition independent, piezoresistive instrument that provides accurate pressure measurement throughout the rough vacuum region.
The HVG-2020A is easy to install, can be configured with an optional touchscreen display to offer a choice of data views, and provides both analog and digital output for process control integration.
- With a wide variety of linear analog output signals to select from, the HVG-2020A is an excellent choice to replace more expensive capacitance manometers.
- Digital output options include RS232 and RS485 via a connection on the top of the gauge. A USB connection is also available on many models to make connection and operation simple.
- Monitor and view data remotely using our free, Microsoft® Windows®-based software and log data to Microsoft® Excel® for comprehensive diagnostics that record how the vacuum behaves over time.
Analog I/O: The HVG-2020A has a 9-pin D-sub connection on top of the gauge that allows an analog output signal to be measured amongst other features. The selected linear analog output signal is proportional to the full-scale range of the sensor (1000 Torr).
Available outputs include: 0-1 VDC, 0-5 VDC, 0-10 VDC, 0-20 mA, and 4-20 mA. The vacuum gauge is factory-configured with one of these outputs “active”, but can be easily changed using the touchscreen interface (if installed), or using digital communication when not configured with a touchscreen. Digital communication with the HVG-2020A will be discussed in greater depth in the next section.
- The 9-pin D-sub connection has Hi and Lo setpoints which are activated when the pressure is above or below the respective setpoint. Additionally, the 9-pin D-sub has a pin for input power and can accept 12-36 VDC. For installations without 12-36 VDC, power can be supplied using a bayonet-style connector at the 24 VDC input connection.
Digital I/O: As mentioned earlier, the HVG-2020A offers a variety of digital communication options in addition to the previously discussed analog choices.
- The micro-USB connection is the simplest method to interface the vacuum gauge and allows it to be directly connected to a PC without the need for adapters or extra wiring.
- The 4-conductor TRRS connection can be used to “daisy-chain” multiple gauges together using RS485 or a standard RS232 communication connection.
- The 9-pin D-sub connection has two pins designated for TTL serial communication.
- LabVIEW™ Drivers
All of these digital communication options (with the exception of TTL) enable PC connection and allow monitoring and viewing of data remotely using our free Microsoft® Windows®-based software. This software has many useful features including data logging and customization / configuration of the vacuum gauge. Digital communication is also used to change the analog output, adjust Hi and Lo setpoint values, stream pressure readings, or change pressure units (among many other functions), when the HVG-2020A is not configured with the optional display.
Touchscreen Display: The most powerful feature of the HVG-2020A is the optional touchscreen display which allows monitoring of pressure measurements in a variety of combinations and graphic representations while operating. The display is powered off the vacuum gauge power supply (no additional power supply needed) and is especially useful for installations in which a remote display would be inconvenient. Five different display modes (shown left to right below) include: Pressure, Pressure and Temperature, Setpoint, Bar Graph, and Pressure over Time. Note that the pressure measurement is always displayed in each mode.

The touchscreen’s Menu Button allows the user to cycle through a selection of submenus to change the screen orientation (should the gauge be mounted in a position other than vertical), zero the gauge (only performed if the system pressure is known to be well below 0.1 Torr), view device information (serial number and firmware level), change the analog output, select RS232 or RS485 and a number of baud rates, and restore the vacuum gauge’s configuration to factory default settings. The straight-forward arrangement of measurements and easy to read display, lets you “see clearly”, similar to 20/20 vision!
Applications and Industries
-
Rough Vacuum Monitoring
- Semiconductor
- Laser Systems
- Chemical Research
- Air Sampling
- Central Vacuum Monitoring
- Oil Reprocessing
- Medical Research